Según la guía ILAC-G24 / OIML D 10 la decisión inicial para determinar el intervalo de recalibración se basa principalmente en un análisis de evaluación de riesgos y debe tener en cuenta, entre otros, los siguientes factores:
a) incertidumbre requerida;
b) tipo de equipo;
c) riesgo de que el equipo de medición exceda la tolerancia;
d) las recomendaciones del fabricante con respecto al equipo de medición;
e) severidad del uso y condiciones ambientales (por ejemplo, condiciones climáticas, vibración, radiación ionizante);
f) frecuencia de las comparaciones con otros patrones de medición o verificaciones intermedias;
g) grado de capacitación del personal operativo; y
h) Requisitos legales.
Análisis de riesgo
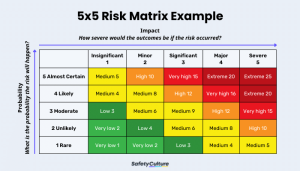
Se debe analizar el riesgo teniendo en cuenta el riesgo de informar resultados que pongan en duda la competencia técnica del laboratorio y los costos asociados con la recalibración frecuente de equipos. En los costos asociados se debe tener en cuenta no solo el costo de la calibración en si, sino todos los costos administrativos y de perdida de oportunidades mientras el equipo esta en recalibración.
Incertidumbre requerida
Una incertidumbre mas baja puede llevar a requerir calibraciones mas frecuentes que incertidumbres mayores. Por ejemplo una SPRT cuya deriva anual esta especificada a 2mK puede ser calibrada cada 2 años si se usa en el calculo de incertidumbre una deriva mayor. Esto puede ser util en casos donde no se requiera una incertidumbre tan baja o cuando por otras razones no se puede bajar la incertidumbre (por ejemplo la homogeneidad del baño liquido no es suficientemente buena).
Tipo de equipo
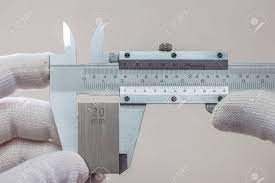
En muchos casos se puede recurrir a bibliografía o experiencia con equipos similares como ayuda para seleccionar la frecuencia de calibración.
Distintos tipos de equipos pueden llevar a distintas frecuencias iniciales de calibración ya sea por recomendación del fabricante o por el fundamento del mismo. Por ejemplo equipos electrónicos en general se sugiere que en primera instancia si se usan en su mejor capacidad deben ser calibrados cada un años, pero equipos no electrónicos como resistores de alto nivel, pistones de balanzas de pesos muertos, pesas o bloques dimensionales pueden calibrarse cada mas tiempo siempre que se usen y mantengan correctamente y tengan verificaciones periódicas.
Riesgo de fuera de tolerancia
Este es posiblemente el criterio mas importante. Para este criterio hay que tener en cuenta el efecto de un fuera de tolerancia sobre la competencia técnica del laboratorio, la reputación del laboratorio en el mercado y el efecto económico en caso de todo esto.
Un fuera de tolerancia en un patrón puede hacer que el laboratorio tenga que repetir calibraciones desde la ultima calibración del equipo, con lo cual es un golpe terrible a la reputación del laboratorio en el mercado y a la confianza que los clientes tienen en el laboratorio y además puede ser terrible economicamente.
Este riesgo se minimiza con verificaciones intermedias planificadas y ejecutadas de forma adecuada y controlando los resultados de los equipos calibrados de clientes. Cuando se percibe en los resultados de los clientes que están dando valores corridos para un lado esto debería disparar una verificación para asegurar que esa tendencia no sea por un error del patron y que sea de los equipos bajo calibración.
La importancia del riesgo dependerá del uso que se le de al equipo y de lo criticas que sean esas mediciones. En el caso de calibraciones hechas para la industria de la salud, alimenticia o alguna otra que tenga consecuencias sobre la salud de la población el riesgo se deberá considerar mas importante.
Recomendaciones del fabricante
El fabricante hace recomendaciones sobre la frecuencia de calibración para mantener la exactitud. Esta frecuencia puede ser modificada para minimizar riesgos o disminuir costos, pero se debe realizar evaluando el costo beneficio.
El fabricante en general realiza exhaustivos ensayos para determinar un tiempo de calibración tal que permita mantener las especificaciones.
Condiciones de uso
Las condiciones de uso deben ser también consideradas para el análisis de riesgo. Cuando un equipo se usa a condiciones extremas el desgaste es mayor y aumenta la posibilidad de fallas y fuera de tolerancia.
Por ejemplo equipos electrónicos usados en camaras de congelado deben tener una frecuencia mayor y se debe tener mas cuidado que con equipos usados a temperaturas sobre 0°C mayormente debido a la condensación que se produce al ser retirado de la cámara y que puede producir desde fallas totales hasta fuera de tolerancias.
Verificaciones intermedias
Un buen programa de verificaciones intermedias disminuye el riesgo y permite incrementar el periodo de calibración. La frecuencia de verificaciones debe ser tal que en caso de detectarse un problema la carga de trabajo para analizar sea razonable.
Las verificaciones intermedias realizadas correctamente permiten aumentar el periodo de calibraciones en algunos instrumentos. El principal problema de las verificaciones es el costo de patrones o elementos adicionales que tengan la suficiente estabilidad para poder ser usado para verificaciones. Ejemplos verificaciones a un costo accesible pueden ser el punto de 0°C para temperatura, resistores Vishay de alta estabilidad, medición con 2 equipos de un mismo ítem.
Una verificación intermedia con resultado satisfactorio puede ser un punto de corte cuando se esta analizando todas las calibraciones que tuvieron problemas por un desvío del patrón.
Grado de capacitación del personal operativo
Personal operativo muy capacitado podría detectar las fallas de los equipos antes en algunas situaciones y frenar para realizar verificaciones.
Por ejemplo un técnico muy formado realizando calibraciones en campo donde varias mediciones dan errores significativos similares para el mismo lado sospechara que hay algún problema y buscara la forma de hacer una verificación en campo.
Requisitos legales
Algunos organismos regulatorios pueden «recomendar» o definir frecuencias de calibración. En esos casos estas son las frecuencias mínimas y si se determina que se debe calibrar cada menos tiempo esto es posible
Determinación del riesgo
Básicamente consiste en determinar cuanto seria el riesgo de fuera de tolerancia usando como entradas los puntos vistos anteriores. Se asume una matriz de 3 entradas con probabilidad de ocurrencia, severidad/impacto y detectabilidad, donde:
Incertidumbre requerida: a menor incertidumbre requerida la probabilidad de ocurrencia va a ser menor.
Tipo de equipo: cuanto mejor es el equipo, mas confianza se le puede tener a que se mantenga en tolerancia por lo tanto la probabilidad de ocurrencia es menor.
Riesgo de fuera de tolerancia: Se define en cuanto afectaría un fuera de tolerancia de ese equipo a la operatoria del laboratorio. Si es un equipo que se usa para muchos clientes el impacto sera mayor, si es un equipo auxiliar que afecta a la incertidumbre en un mínimo el impacto será bajo.
Recomendaciones del fabricante: Si se siguen las recomendaciones del fabricante o se calibra más frecuentemente que lo recomendado la probabilidad de ocurrencia será intermedio para bajo. Los buenos fabricantes especifican para que el equipo no falle durante el periodo recomendado.
Condiciones de uso: un uso a temperatura, vibraciones u otro tipo de condiciones extremas incrementará el la probabilidad de ocurrencia.
Verificaciones intermedias: cuanto mas y mejores verificaciones intermedias tenga el laboratorio mayor será la detectabilidad. Un buen programa de verificación intermedia va a minimizar mucho el riesgo por tener una alta detectabilidad.
Grado de capacitación del personal operativo: Personal técnico altamente capacitado también incrementa la detectabilidad (en menor medida que las verificaciones intermedias).

Evaluación de costo del riesgo vs costo de calibración
Como en toda determinación de riesgo se debe evaluar si podemos aceptar el riesgo o no comparando el costo derivado del riesgo con el costo de incrementar una frecuencia de calibraciones para ver si esto es posible.
El costo del riesgo incluye repetición de trabajos, investigaciones de acciones correctivas, confianza de los clientes, reputación del laboratorio en el mercado, etc.
El costo de calibración no solo se limita al costo de la calibración, sino que también se debe tener en cuenta el costo de no poder realizar trabajos durante el periodo donde el equipo este en calibración y el costo administrativo (ordenes de compra, envío, pago, verificación de resultados, etc.)
Un comentario en “Determinación de frecuencia de calibración”